Archivio 2019
PRO₂AIR Pre-PUR® Polyurethan membrane tube diffuser made from polyurethane: increased safety, lower operating costs
NORRES Schlauchtechnik manufactures innovative membrane tube diffusers from polyurethane
NORRES, the Gelsenkirchen based hose manufacturer, recently unveiled an innovative Pre-PUR® membrane tube diffuser made from premium polyurethane. All the other tube diffusers currently available in the market often have a shorter lifetime and are much more sensitive to dynamic loads owing to their inferior raw materials. In many cases, their mechanical properties deteriorate during the course of their service life, leading to premature damage such as cracks in the diffuser membrane. Some of these diffusers additionally suffer from a significant increase in pressure loss as they grow older because the softener leaches out. With the new PRO₂AIR Pre-PUR® made from premium polyurethane this is no longer possible: it is absolutely free of softeners and impresses with its extreme flexibility and mechanical strength under dynamic loads.
The innovative PRO₂AIR Pre-PUR® membrane tube diffuser made from premium polyurethane was recently added to the portfolio of the NORRES Schlauchtechnik Environmental Solutions Business Unit. It is used for intermittent, fine-bubble, compressed air aeration (nitrification / denitrification) as well as continuous aeration. The membrane material exhibits very good resistance to municipal wastewater according to the latest version of the DWA-M 115 Advisory Leaflet. Thanks to the Pre-PUR® premium polyurethane, the new membrane tube diffuser is characterised by high tensile strength and tear resistance, and is also remarkably durable and robust. Its extreme flexibility and mechanical strength under dynamic loads mean increased reliability, an extended service life and hence lower operating costs. Other tube diffusers currently available in the market tend to form a kink edge in intermittent operation; the resulting permanent kinking can be a primary cause of damage in the long term. If damage of this kind occurs, sludge can get into the system; significantly more air escapes from a defective or ruptured diffuser than from an intact one. There is a rapid decrease in oxygenation, leading to reduced oxygen transfer efficiency and impacting the diffuser's reliability. Previous attempts to improve the poor resistance to permanent kinking of the materials traditionally employed using asymmetric supporting bodies have proved not only sub-optimal but also expensive.
The new NORRES PRO₂AIR Pre-PUR® membrane tube diffuser resist permanent kinking better than ever before. In a De Mattia test, based on DIN ISO 132, PRO₂AIR Pre-PUR® membrane tube diffuser achieved up to four times better resistance to permanent kinking than other materials. The tube diffuser membrane of the innovative PRO₂AIR is absolutely free of softeners and therefore permanently elastic: there is no hardening or embrittlement of the membrane. What's more, the new PRO₂AIR Pre-PUR® made from premium polyurethane has optimised slit perforation. The membrane tube diffuser is perforated using a specially developed technique that assures optimal quality consistency. All tools and materials utilised were explicitly developed for, and tailored to, the PRO₂AIR Pre-PUR®. This guarantees a uniform bubble pattern and optimal oxygenation efficiency across the complete specific air flow range. It goes without saying that the new PRO₂AIR Pre-PUR® is permanently resistant to microbial attack and hydrolysis, and the minimal maintenance requirement is a further point in its favour. Last but not least, a high pressure loss and low oxygen transfer efficiency result in high energy consumption. Many popular systems offer either a low pressure loss or a high oxygen transfer rate, but not both. The PRO₂AIR Pre-PUR® membrane tube diffuser successfully combines low pressure loss with a very high oxygen transfer rate and transfer efficiency – yet another feature that helps keep energy requirements and operating costs to a minimum.
NORRES, one of the leading manufacturers of industrial hoses and hose systems, can look back on a history of more than 120 years. Thanks particularly to its own R&D and Engineering departments, the hose producer – which has served the plastics industry almost from the outset – is in a position to respond flexibly and spontaneously to customer needs. This first-class support has been the source of many exciting innovations in the past.
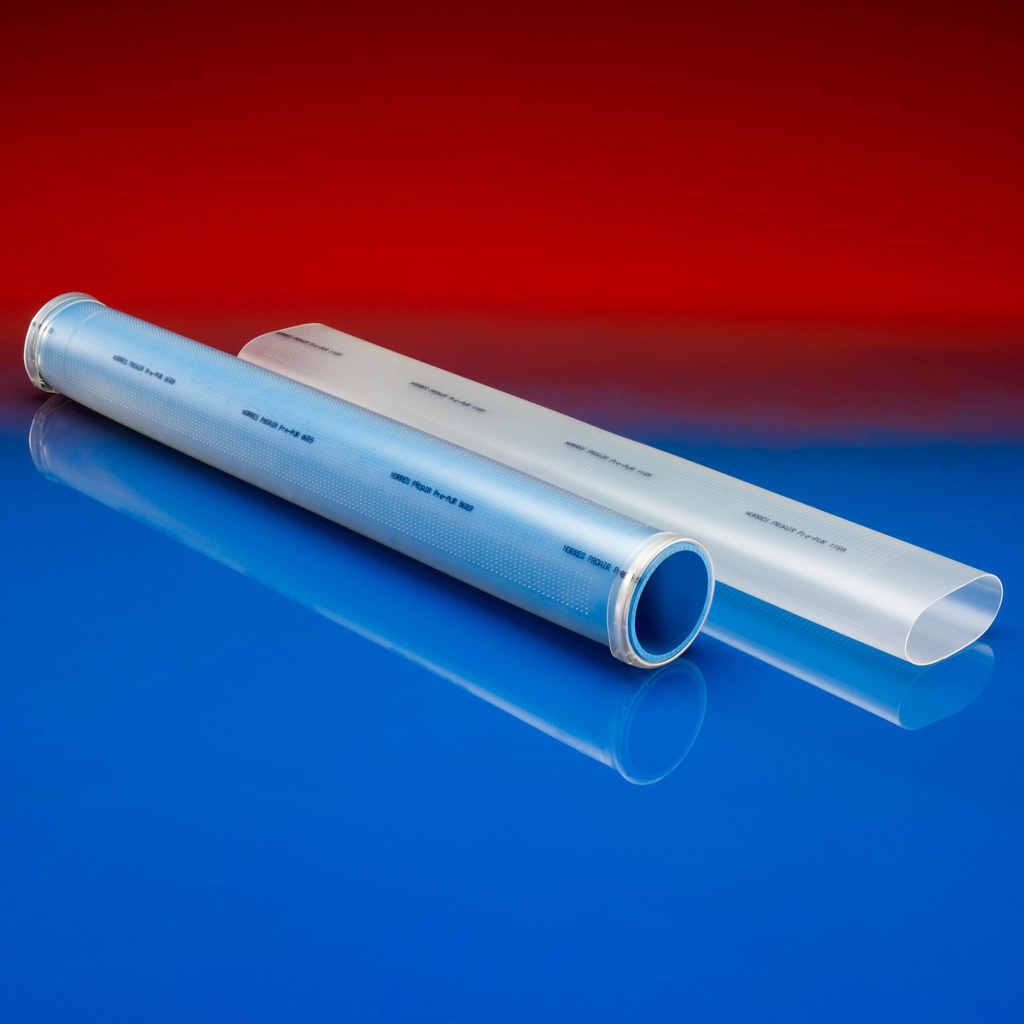